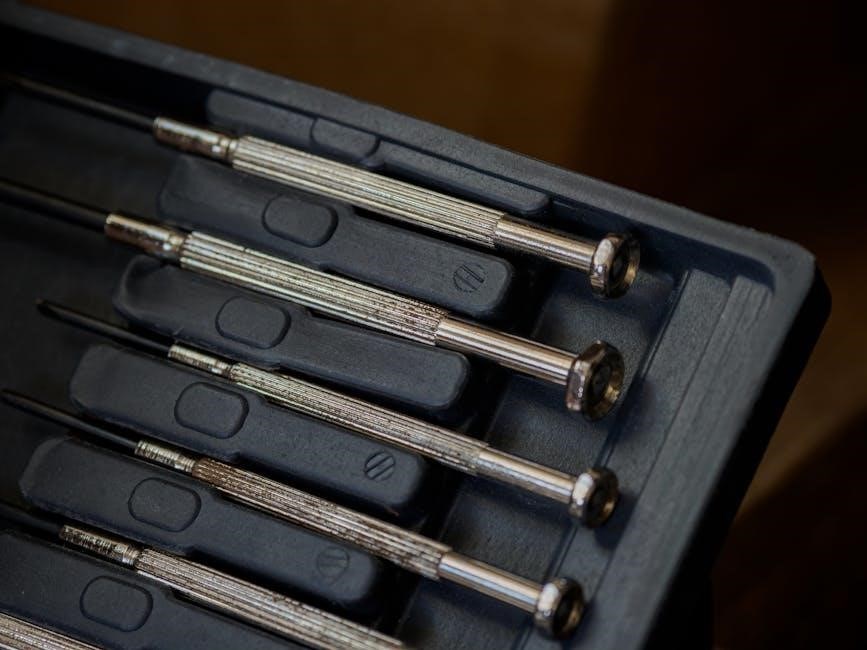
briggs stratton valve guide repair kit
Briggs Stratton valve guide repair kits are designed to restore engine performance by addressing worn or damaged valve guides, ensuring proper valve alignment and sealing.
Overview of the Valve Guide Repair Process
The repair process involves removing the worn valve guide and installing a new one using specialized tools like reamers and guide bushings. Proper measurement is critical to ensure the new guide fits precisely. The process typically includes cleaning the area, reaming the worn guide to size, and pressing in the replacement part. It’s important to follow the manufacturer’s instructions to avoid further damage. This method restores proper valve alignment and sealing, improving engine performance and reducing emissions.
Importance of Valve Guide Maintenance
Proper valve guide maintenance is crucial for ensuring optimal engine performance, preventing oil leakage, and reducing emissions. Worn guides can lead to poor compression, increased oil consumption, and reduced power output. Regular inspection and timely repairs help avoid costly damage to the engine head or cylinders. By addressing valve guide issues early, users can extend the lifespan of their Briggs Stratton engine, maintain its efficiency, and prevent premature wear on other critical components.
Symptoms of Worn Valve Guides in Briggs Stratton Engines
Increased oil consumption, misfires, bent pushrods, and poor engine performance are common symptoms of worn valve guides, indicating the need for immediate repair or replacement.
Common Issues Caused by Damaged Valve Guides
Damaged valve guides can lead to excessive oil consumption, misfires, and bent pushrods. Worn guides often cause poor engine performance, reduced power, and increased emissions. Over time, this can result in valve stem seal failure and further engine damage, requiring costly repairs. Addressing these issues promptly is essential to maintain engine reliability and efficiency.
How to Diagnose Valve Guide Problems
Diagnosing valve guide issues involves checking for excessive oil consumption and blue smoke from the exhaust. Inspect the valve face for irregular seating patterns and measure guide clearance using specialized tools. Look for bent pushrods or valve stem wear. Reaming the guides with specific tools, such as reamer 19183, can help assess wear. These steps help identify damaged guides needing repair or replacement to restore engine performance and prevent further damage.
Tools and Materials Needed for Valve Guide Repair
Essential tools include a valve guide reamer (e.g., part 19183) and guide bushing (e.g., 19192). Materials like valve guide bushings, seals, and the repair kit are required.
Essential Tools for the Repair Process
The repair process requires specialized tools like a valve guide reamer (e.g., part 19183) and guide bushing (e.g., 19192) to ensure proper fitment and alignment. A drill press may be necessary for precise drilling, while a micrometer helps measure guide clearance accurately. Additionally, a set of wrenches, punches, and a valve spring compressor are crucial for disassembling and reassembling engine components. Using the correct tools ensures a professional-grade repair, maintaining engine performance and reducing future issues.
Recommended Materials and Replacement Parts
Essential materials include valve guide bushings (e.g., part 230655) and reamers (e.g., 19183) for precise resizing. Replacement parts like valve seats, springs, and seals are often required. For severe damage, a complete head assembly replacement may be necessary, which includes valves and related components. A Neway valve seat kit is recommended for accurate resurfacing. Ensure all parts are OEM-compatible or high-quality alternatives to maintain engine performance and durability. Proper materials guarantee a long-lasting repair and prevent future valve guide issues.
Step-by-Step Guide to Repairing Valve Guides
Use specialized tools like reamers and bushings to remove and replace worn valve guides, ensuring precise alignment and sealing for optimal engine performance and longevity.
Preparing the Engine for Repair
Begin by draining engine fluids and allowing the motor to cool. Disconnect the spark plug wire and remove components like the carburetor and valve cover. Use a torque wrench to remove head bolts carefully. Clean the cylinder head surface and surrounding areas to ensure a debris-free workspace. Inspect for additional damage and gather all necessary tools and replacement parts. Proper preparation ensures a smooth and effective repair process for the valve guides.
Installing the Valve Guide Repair Kit
Install the new valve guide by first drilling out the old guide using a drill press and specialized reamers. Ensure the new guide aligns perfectly with the valve seat. Use a torque wrench to secure it firmly, following the manufacturer’s specifications. Apply a small amount of engine oil to the new guide for lubrication. Proper installation ensures the valve operates smoothly and prevents future damage. Always refer to the repair manual for precise measurements and torque settings to avoid misalignment or over-tightening.
Cost Analysis and Benefits of Using a Repair Kit
Using a repair kit is cost-effective, offering significant savings compared to replacing the entire head assembly. It ensures long-term engine performance and reliability.
Comparing Repair Kit Costs to Replacing the Head Assembly
Repair kits are significantly more cost-effective than replacing the entire head assembly, which can be expensive. A repair kit offers a practical solution for restoring valve guide functionality, often at a fraction of the cost. This approach prevents further engine damage and ensures optimal performance without the financial burden of replacing the whole head. It’s a viable option for extending engine lifespan while maintaining reliability and efficiency.
Long-Term Benefits ofRepairing Valve Guides
Long-Term Benefits of Repairing Valve Guides
Repairing valve guides offers long-term benefits, including improved engine performance, reduced oil consumption, and minimized emissions. It prevents further damage to engine components, ensuring reliability and extending lifespan. A properly repaired valve guide also enhances combustion efficiency and maintains optimal engine power. Regular maintenance and timely repairs can significantly delay the need for major overhauls, saving time and money over time. This proactive approach ensures smoother operation and reduces the risk of unexpected engine failures.
Troubleshooting Common Issues After Repair
Identify and address leaks, misaligned guides, or improper seating by inspecting seals, re-tightening connections, and verifying alignment. Ensure all components meet specifications for optimal engine performance and durability.
Addressing Leaks or Misaligned Guides
Leaks or misaligned guides after repair can be resolved by rechecking valve seat alignment and ensuring proper sealing. Inspect the valve guide bushings for correct installation and tighten any loose connections. Use a leak-down test to identify air leaks, and verify guide alignment with the valve stem. If misalignment persists, consult the repair manual for reamers like part number 19183 and bushing 19192 to achieve accurate realignment. Proper installation ensures long-term engine performance and prevents further damage.
Ensuring Proper Engine Performance Post-Repair
After installing the valve guide repair kit, ensure the engine runs smoothly by checking for leaks and testing under load. Verify proper valve alignment and seating, and inspect the valve guide bushings for correct installation. Use Briggs & Stratton-recommended tools like reamer 19183 and bushing 19192 to maintain precise alignment. Regular inspections and timely adjustments will help maintain optimal engine performance and prevent future issues. Always follow the repair manual guidelines for long-term reliability.
Maintenance Tips to Prevent Future Valve Guide Damage
Regularly inspect valve guides for wear, clean debris, and ensure proper alignment. Replace worn bushings promptly and verify tightness of all components to prevent future issues.
Regular Inspection and Cleaning Practices
Regular inspection of valve guides is crucial to prevent damage. Use a reamer and guide bushing, like part numbers 19183 and 19192, to check for wear. Ensure the valve stem moves smoothly without looseness or excessive play. Clean debris from the valve area and ream out worn guides to maintain proper alignment. Always consult the Briggs repair manual for specific part numbers and measurements; Proper maintenance extends engine lifespan and prevents performance issues.
Best Practices for Extending Engine Lifespan
Regularly inspect valve guides and replace worn or damaged parts promptly. Use the correct reamers and guide bushings, such as part numbers 19183 and 19192, to maintain proper alignment. Always follow the Briggs repair manual for specific instructions and measurements. Replace the head assembly if valve guides cannot be repaired. Proper maintenance ensures optimal performance, reduces emissions, and extends engine lifespan. Addressing issues early prevents costly repairs and keeps your engine running efficiently for years.
Briggs Stratton valve guide repair kits provide an effective solution for restoring engine performance and preventing future damage. Proper installation and maintenance are key to long-term reliability and longevity.
Importance of Proper Installation and Maintenance
Proper installation and maintenance of Briggs Stratton valve guide repair kits are crucial for ensuring optimal engine performance and preventing future damage. Using the correct tools, such as reamers and guide bushings, ensures precise alignment and sealing. Regular inspections and cleaning help maintain valve guide integrity, preventing issues like leaks or misalignment. Following the manufacturer’s guidelines and investing in quality materials guarantees long-term reliability and extends the engine’s lifespan, avoiding costly repairs down the line.
Case Studies of Successful Valve Guide Repairs
Successful valve guide repairs using Briggs Stratton kits have been documented in various applications, such as lawn mowers and small engines. For instance, a Simplicity Citation zero-turn mower experienced restored performance after a valve guide repair. Another case involved a customer saving significant costs by repairing instead of replacing the head assembly. These examples highlight the effectiveness of repair kits in extending engine lifespan and maintaining optimal functionality, proving their value in practical scenarios.