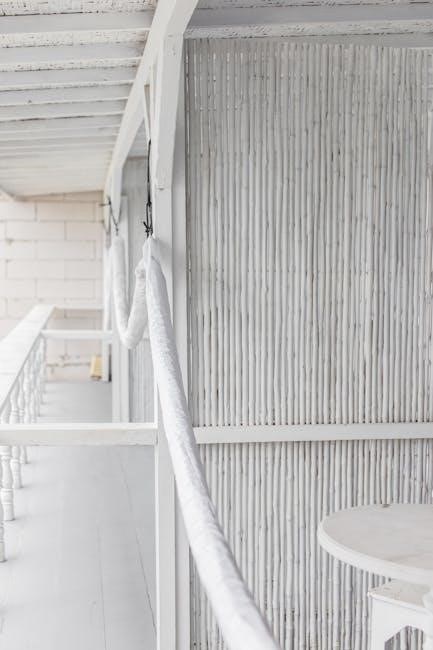
linear guide rail
Linear guide rails are essential components enabling smooth, precise motion in machinery and automation, ensuring efficient operation across various industrial applications.
1.1 Definition and Overview
Linear guide rails are mechanical components designed to enable smooth, precise motion along a linear path. They consist of a rail and a carriage or slider, which move with minimal friction. These systems are crucial in machinery and automation, providing stable and consistent movement for various applications. Available in types such as ball bearing, roller, and plastic, they cater to different load capacities and operational requirements, ensuring efficient performance in industrial and technical environments.
1.2 Importance in Machinery and Automation
Linear guide rails play a pivotal role in machinery and automation by ensuring precise and smooth motion, which is critical for maintaining operational efficiency. They minimize wear and tear, reduce noise, and enhance the overall performance of systems. In applications like CNC machines and robotics, their reliability and durability are essential for achieving high production standards and consistent output quality, making them indispensable in modern industrial setups.
Types of Linear Guide Rails
Linear guide rails are categorized into ball bearing, roller, and plastic types, each offering distinct advantages in terms of load capacity, precision, and operational smoothness.
2.1 Ball Bearing Linear Guide Rails
Ball bearing linear guide rails are widely used for their high precision and smooth motion. They utilize recirculating ball bearings to minimize friction and maximize load capacity. These rails are ideal for applications requiring high accuracy and durability, such as CNC machines and robotics. Their design allows for easy installation and maintenance, making them a popular choice in industrial automation. Proper lubrication ensures long-term performance and prevents wear.
2.2 Roller Linear Guide Rails
Roller linear guide rails use cylindrical rollers instead of balls, offering higher load capacity and rigidity. They are ideal for heavy-duty applications requiring robust support. Their design minimizes deformation under heavy loads, making them suitable for industrial machinery and construction equipment. While they may produce more noise than ball-bearing types, rollers provide exceptional durability and stability in harsh environments. Regular maintenance is crucial to ensure optimal performance and extend lifespan in demanding conditions.
2.3 Plastic Linear Guide Rails
Plastic linear guide rails are lightweight, corrosion-resistant, and ideal for low-load applications. They offer smooth motion with minimal noise and are cost-effective. Often used in 3D printers, they provide sufficient precision for lightweight tasks. However, they lack the durability of metal rails and may wear down quickly under heavy use. Maintenance is simplified due to self-lubricating properties, making them a practical choice for hobbyists and non-industrial projects requiring reliable, quiet operation without the need for heavy-duty performance.
Key Characteristics of Linear Guide Rails
Key characteristics of linear guide rails include high load capacity, durability, and smooth motion. They are essential for machinery and automation, ensuring low friction and resistance to wear, which maintains operational efficiency and extends lifespan.
3.1 Load Capacity and Durability
Linear guide rails are designed to handle significant loads while maintaining structural integrity and operational reliability. Their durability ensures long-term performance in demanding environments, with materials like hardened steel providing resistance to wear and tear. Proper installation and maintenance further enhance their lifespan, making them critical components in industrial machinery and automation systems. High load capacity and durability are essential for ensuring smooth, consistent motion and minimizing downtime in production processes.
3.2 Precision and Accuracy
Linear guide rails are engineered to deliver high precision and accuracy, ensuring minimal deviation in motion. Their advanced design and materials, such as hardened steel or ceramic coatings, minimize wear and optimize performance. This precision is crucial for applications requiring exact positioning, such as CNC machines and robotic systems. By maintaining consistent and reliable motion, linear guide rails enhance the overall accuracy and efficiency of industrial and automation processes, making them indispensable in high-precision manufacturing environments.
Linear guide rails are designed to ensure smooth motion and minimize noise, enhancing operational efficiency. Advanced materials like hardened steel and ceramic coatings reduce friction, while ball or roller bearings promote quiet operation. Lubrication systems further enhance smoothness, making these rails ideal for applications requiring low noise, such as robotics and 3D printing. The combination of precise engineering and high-quality materials ensures consistent, noise-free performance, making linear guide rails essential for modern machinery and automation systems.
Applications of Linear Guide Rails
3.3 Smoothness and Noise Reduction
Linear guide rails are designed to ensure smooth motion and minimize noise, enhancing operational efficiency. Advanced materials like hardened steel and ceramic coatings reduce friction, while ball or roller bearings promote quiet operation. Lubrication systems further enhance smoothness, making these rails ideal for applications requiring low noise, such as robotics and 3D printing. The combination of precise engineering and high-quality materials ensures consistent, noise-free performance, making linear guide rails essential for modern machinery and automation systems.
4.1 CNC Machines and Machining Centers
Linear guide rails are crucial in CNC machines and machining centers, ensuring high precision and smooth motion for accurate cutting and drilling operations. Their robust design handles heavy loads and high speeds, making them ideal for demanding industrial tasks. Proper lubrication and maintenance are essential to maintain optimal performance and extend lifespan, ensuring consistent productivity in manufacturing processes. These rails enable precise control, reducing errors and improving overall machining efficiency. Their reliability makes them indispensable in modern CNC systems.
4.2 Robotics and Automation Systems
Linear guide rails play a vital role in robotics and automation systems by enabling smooth, precise motion for tasks like assembly, material handling, and pick-and-place operations. Their high load capacity and durability make them suitable for heavy-duty robotic applications. Low friction and consistent movement ensure efficient operation, reducing wear and tear. These rails are essential for maintaining accuracy and reliability in automated systems, allowing robots to perform repetitive tasks with high precision and minimal downtime, enhancing overall production efficiency and consistency.
4.3 3D Printing and Additive Manufacturing
Linear guide rails are crucial in 3D printing and additive manufacturing for ensuring precise, smooth motion. They enable accurate positioning of print heads, minimizing layer shifting and improving print quality. Durable and low-maintenance, these rails withstand the repetitive movements required in additive manufacturing. Their quiet operation reduces noise, and their compact design allows for space efficiency in 3D printers. Plastic linear guides, such as those from Igus, are often used for their lightweight and cost-effective properties, making them ideal for DIY and industrial 3D printing applications.
Installation and Maintenance
Proper installation ensures alignment and stability, while regular lubrication prevents wear. Cleanliness is crucial to avoid contamination and maintain smooth operation over time.
5.1 Best Practices for Installation
Proper installation of linear guide rails ensures optimal performance and longevity. Begin by cleaning the rail surfaces thoroughly to remove dirt or grease. Use alignment tools to ensure the rail is straight and level, preventing uneven wear. Secure the rail firmly using the recommended fasteners, avoiding overtightening. Apply a thin layer of lubricant as specified by the manufacturer. Finally, test the system under light load to confirm smooth operation before full implementation.
5.2 Regular Maintenance and Lubrication
Regular maintenance is crucial for extending the lifespan of linear guide rails. Clean the rails periodically to remove dirt and debris, which can cause wear. Apply the manufacturer-recommended lubricant to minimize friction and prevent corrosion. Inspect the rails for signs of wear or damage and replace components as needed. Proper lubrication ensures smooth operation and reduces the risk of premature failure, maintaining the system’s efficiency and reliability over time.
Factors to Consider When Selecting Linear Guide Rails
Key factors include environmental conditions, load and speed requirements, and budget constraints to ensure optimal performance and durability in industrial applications.
6.1 Environmental Conditions
Environmental factors like temperature, humidity, and exposure to chemicals or dust significantly impact the choice of linear guide rails. Harsh conditions may require specialized materials or protective coatings to prevent corrosion or contamination. For instance, in high-temperature environments, heat-resistant materials are essential to maintain stability and performance. Similarly, in cleanroom settings, guide rails must minimize particle emission to avoid contamination. Proper consideration ensures durability and reliability in diverse applications, from industrial machinery to precision instruments.
6.2 Load and Speed Requirements
Load and speed requirements are critical factors in selecting linear guide rails. Higher load capacities are needed for heavy-duty applications, while lower loads may suffice for lighter tasks. Speed requirements also influence the choice, as excessive velocity can compromise precision and longevity. The type of rail and its material must align with the operational demands to ensure optimal performance. Balancing load, speed, and precision is essential for achieving reliable and efficient motion in machinery and automation systems.
6.3 Cost and Budget Constraints
Cost and budget constraints significantly influence the selection of linear guide rails. While high-performance rails offer durability and precision, they can be expensive. Plastic guides, like those from Igus, provide a cost-effective alternative for lighter applications. Balancing budget with performance is crucial to avoid over-spending or compromising on quality. Evaluating long-term maintenance and replacement costs also helps in making economical decisions, ensuring the chosen rail meets both financial and operational needs effectively.
Advantages and Disadvantages
Linear guide rails offer high precision and durability but may experience noise and wear over time, affecting performance in demanding applications and environments.
7.1 High Precision and Smooth Operation
Linear guide rails are renowned for their ability to provide high precision and smooth operation, making them indispensable in applications requiring accurate and consistent motion control. Their advanced designs minimize friction and ensure stable movement, which is critical for machinery and automation systems. This smooth operation not only enhances productivity but also reduces the risk of mechanical stress and wear, ensuring optimal performance in industrial and manufacturing environments. Their precision is unmatched, delivering reliable results in demanding conditions.
7.2 Durability and Long Lifespan
Linear guide rails are designed for exceptional durability, with robust materials like steel or aluminum ensuring long-term reliability under heavy loads. Proper lubrication and maintenance extend their lifespan, minimizing wear and tear. High-quality rails withstand demanding conditions, offering consistent performance over years. Their rugged construction and precise engineering make them a cost-effective solution, reducing downtime and extending operational life in industrial and manufacturing settings.
7.3 Potential for Noise and Wear
Linear guide rails can experience noise and wear over time, particularly if improperly lubricated or exposed to heavy loads. Plastic guides may develop friction, leading to operational noise, while metal components can degrade without maintenance. Regular lubrication and inspection are crucial to mitigate these issues, ensuring smooth operation and extending the rail’s lifespan. Addressing these factors early helps maintain performance and prevents premature wear, which can lead to system downtime and increased maintenance costs. Proper care is essential for optimal functionality.
Common Issues and Solutions
Linear guide rails often face issues like noise, vibration, and wear due to improper lubrication or misalignment. Regular maintenance and alignment checks can resolve these problems effectively.
8.1 Noise and Vibration Problems
Noise and vibration issues in linear guide rails often arise from improper lubrication, misalignment, or worn components. Regular lubrication and alignment checks can mitigate these problems. Additionally, using noise-reducing materials and ensuring proper installation can help minimize vibrations, enhancing overall system performance and longevity. Addressing these issues promptly prevents further damage and ensures smooth operation in machinery and automation systems.
8.2 Jamming or Sticking Issues
Jamming or sticking in linear guide rails can occur due to misalignment, contamination, or insufficient lubrication. These issues disrupt smooth motion and may damage the system. Proper alignment during installation and regular cleaning are crucial to prevent debris buildup. Applying the right lubricants ensures reduced friction and smooth operation. Addressing these problems early can prevent costly repairs and downtime, ensuring optimal performance in industrial and automated applications.
8.3 Wear and Tear Over Time
Wear and tear on linear guide rails can result from prolonged use, heavy loads, or harsh environmental conditions. Regular lubrication and cleaning help minimize friction and extend lifespan. Inspecting rails periodically ensures early detection of wear. Replacing worn components promptly prevents further damage. Addressing wear proactively maintains system performance and reliability, avoiding costly downtime in industrial and automated applications. Proper maintenance is key to ensuring longevity and optimal functionality.
Linear guide rails are vital for precise motion in machinery, balancing performance and maintenance needs, and their versatility underscores their essential role in modern technological advancements.
9.1 Summary of Key Points
Linear guide rails are crucial for precise motion in machinery, offering high accuracy and durability. Available in ball, roller, or plastic types, they cater to diverse applications like CNC machines, robotics, and 3D printing. Their selection depends on factors such as load capacity, speed, environmental conditions, and budget. Proper installation and maintenance ensure optimal performance, making them indispensable in modern automation and manufacturing. This summary highlights their significance and versatility across various industrial uses.
9.2 Future Trends in Linear Guide Rail Technology
Future trends in linear guide rail technology include advancements in materials science, smart automation, and integration with quantum computing. Innovations like self-lubricating surfaces and adaptive systems are expected to enhance durability and efficiency. AI-driven designs will optimize performance for specific applications, while eco-friendly materials align with sustainability goals. These advancements promise to revolutionize industries, enabling smoother, quieter, and more precise motion systems across robotics, manufacturing, and beyond, setting new standards for industrial automation.